Building A Watch Brand Episode 12: Ultra-Hard Coating And Other Updates
Several specialized manufacturers are currently hard at work producing the parts for the samples of my VPC Type 37HW. Everything we have worked on over the past year is coming together as we speak. To say that fills me with a mix of anxiety and excitement is an understatement. We have, however, fine-tuned a few details still. And, I have an exciting new feature to announce — an ultra-hard coating on the entire case, bracelet, and clasp.
The latter is something I have been silently working on for almost the entire year. There are many different options out there, but it isn’t quite as straightforward as ticking a box on an order form. So I kept it quiet until I was completely certain of what I could offer. Let’s get into it.
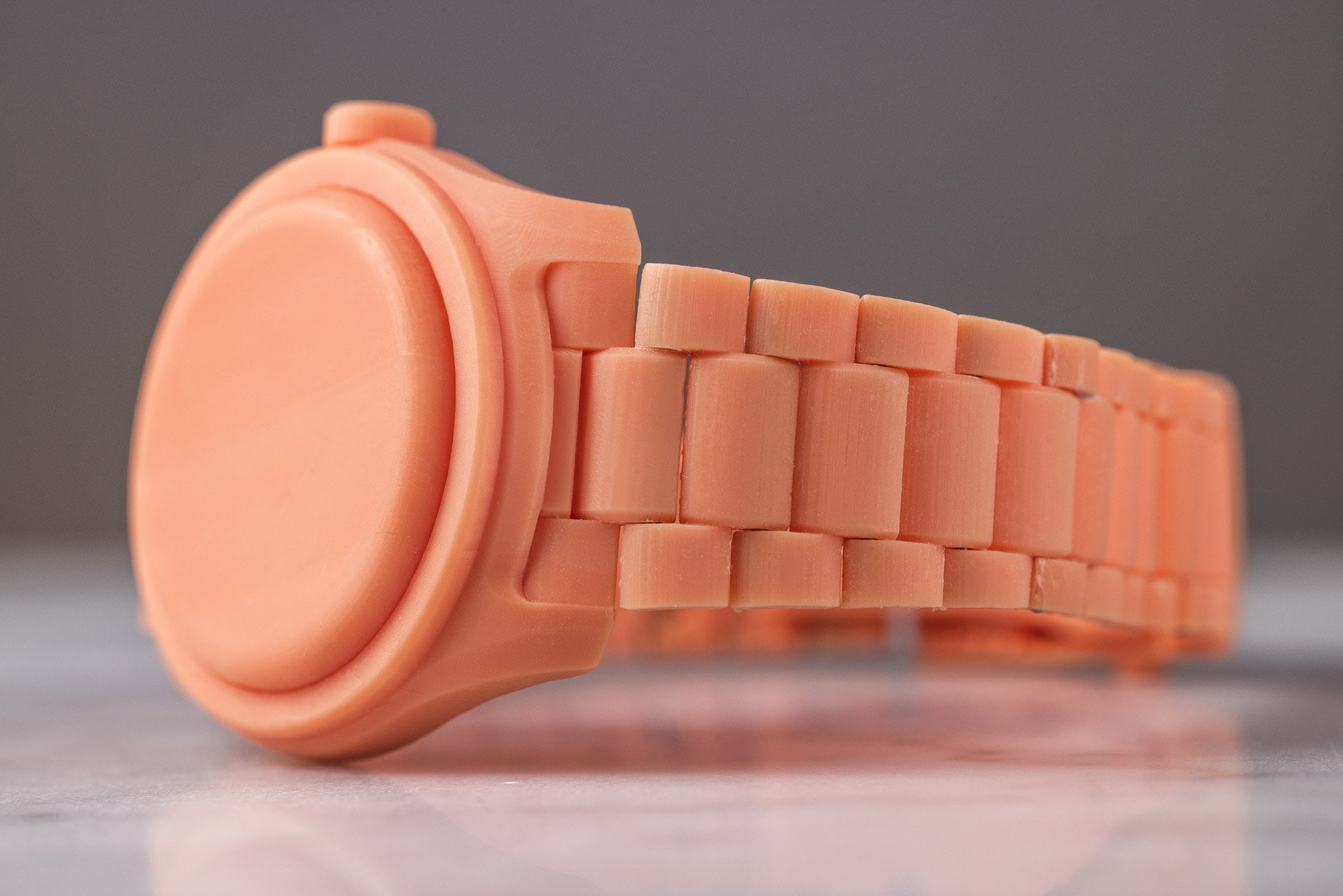
The final pre-production 3D print, now with an articulating bracelet. The end links will sit flush with the lug tips on the real deal.
An ultra-hard coating for the VPC Type 37HW
I have always been amazed that surface-hardening/coating technologies were predominantly applied to tool watches. For me, the sportier the watch, the less I mind a scratch or two. It is the refined, elegant watches that I want to keep pristine. The VPC Type 37HW is a do-it-all watch, combining the sporty and the elegant. I don’t mind if such a watch starts showing its age at some point, but I prefer it to look neat for as long as possible.
So I started looking into hardening technologies. I have spoken to many different companies that offer different ways of doing it, and I have been testing samples of regular and hardened 316L stainless steel. Crucially, I have also been lobbying with manufacturers.
What I didn’t realize in the beginning was that case makers and assemblers are not keen on this at all. They don’t want to send their work off to a surface-treating company before assembly. Their biggest worry is that the tolerances will be compromised in the process. Who is responsible for water resistance when the parts have been handled and processed by different parties? In typical “Mr. Van Straaten, we are really doing you a big favor by accepting you as a client” fashion, I heard “no” a lot. Luckily, that only motivated me to push harder. I ended up with ambitious and forward-thinking suppliers, which is precisely what I need. I cannot work with people who only think about problems and limitations, so I don’t.
Ultra-hard coating versus other surface treatments
Two very promising treatments involved changing the molecular composition of a gradual outer layer of the steel. I tested one with a raised carbon content and one with a higher chrome content. These two methods offer the greatest protection against scratches as they cannot wear off. The big downside is that they both have a slight dulling effect. The steel looks a bit cloudy after treatment. The effect is negligible for industrial use but significant on a finely finished watch.
There were two solutions. One was to make the entire case and bracelet bead-blasted in finish. Brands like Sinn take this approach. With fine polishing, chamfering, and brushing key to the design, this was no option for me. The other was to finish the watch, harden it, and then refinish it. This would, however, take away some of the hardened material. There would be no way to know if and to what degree the refinished surfaces would still be hardened afterward. In theory, one part of the bezel, for instance, could be fully hardened, and another not at all. That isn’t ideal, especially considering the costliness of this approach.
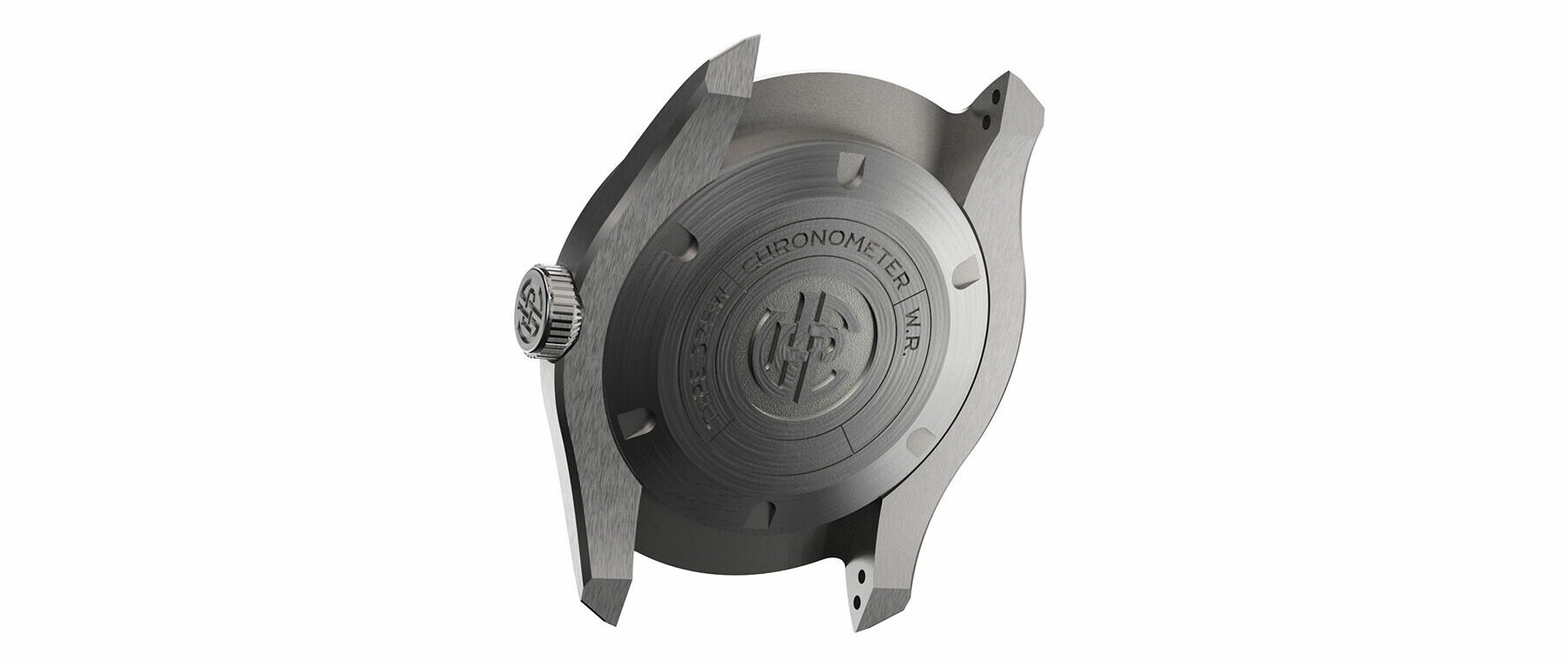
The underside of the mid-case will receive a nice polished chamfer too. The quality experience shouldn’t stop at the front.
The ideal solution turned out to be the ultra-hard coating of the watch. The application process is similar to PVD or DLC, but the result is completely invisible. Simplified, you could regard it as a protective lacquer, except it doesn’t show as such. Seiko’s Diashield is a prime example. It is rumored to be around 500 Vickers in hardness. The Type 37HW’s coating will be between 1,800 and 2,000 Vickers. By comparison, untreated 316L is around 150 Vickers. I have shared a demonstration video on my Instagram with a piece that was coated at 800 Vickers hardness.
Busting some myths about ultra-hard coating
It is good to understand that a watch with an ultra-hard coating isn’t scratchproof. If you put your back into it, you will break through, as I have explained in this earlier article. The goal, however, is to slow down the accumulation of very fine scratches. Think, for instance, of that hazy cloud of micro scratches on your clasp, even from just working at a wooden desk. That will take significantly longer to show on the upcoming Type 37HW. Rest assured, your VPC will age, but it will take longer.
The coating will remain invisible at all times. Even if it were compromised, it would not flake like older black-coated watches do.
Another crucial benefit is that the watch can still be refinished at all times, using normal equipment and the normal process. Your watchmaker may have to spend slightly more time on each surface, but it can be done without issue. In short, if you weren’t told, you probably wouldn’t even know that the coating was there, except that you may notice that the watch remains pristine for much longer than other watches. It is an additional feature that I value highly, so I am excited to offer it on the VPC Type 37HW.
The bezel will be slightly narrower
Another significant update besides the ultra-hard coating is that the flat, vertically brushed bezel got a little bit narrower. Last time, I already shared the slightly thicker sapphire that we needed to use to attain a 120m water resistance rating. Well, it turns out we also need some additional width at the base of the crystal to maintain the over-engineered ruggedness that I am after.
There were three options. One was to shrink the dial, which would throw the entire balance of the design out of whack. Another was to make the watch bigger. After all the effort we put into the perfect proportions, that was never on the table for me. The third was to take the required meat from the bezel. That turned out to be the most elegant solution, where the measurement affects the vibe of the watch a bit but not the balance. If anything, the balance may be slightly better now. Overall, it boosts the elegance in favor of the boldness by a fraction.
I know that the wide bezel was a point of contention with some of my followers. Surely, the narrower bezel is less divisive and will please a broader audience. It wasn’t intended as such, but sometimes you have to accept a happy coincidence. For me, it took a little getting used to, but I prefer the narrower bezel now. If there were any small compromises that I had to make, this is one I can live with.
Some delays in sample production
Now, the previous Building A Watch Brand article came out two months ago. The estimate at that time was three months until I would have the working samples. Unfortunately, we ran into some hurdles. It is a “three steps forward, two steps back” kind of process after all.
My dial maker had some issues with the blue and green dial colors. The way it was, they would come out quite a bit brighter and more vibrant than in the renders. As you may know, Max and I spent countless hours searching for the perfect hues of subdued, versatile green and blue. Understanding the effects of the production process a little better, we had to recalibrate. After some back and forth, I fully expect to get the perfect hues now.
The other issue was our dial printing. As explained earlier, we opted for minimal text, our fully tailor-made “Venustas” typeface, and a wordmark inspired by early watchmaking rather than a logo. The pad printers expressed some worries about legibility. To be 100% sure, we took a step back and did a bunch of testing. We have made some small tweaks to ensure the wordmark will be legible while remaining as small as possible. The “Swiss Made” signature does not have to be legible without a loupe, as long as it prints cleanly. That is now all secured. Unfortunately, these two challenges have added several weeks to our timeline. I now expect to have the samples in about two months from now. Hopefully, I can go back to decent nights of sleep by then!
Getting the VPC Type 37HW on watch lovers’ wrists
That, naturally (even if a little prematurely here) leads me to the final act of building a watch brand — getting the watch on watch lovers’ wrists. If the samples turn out, say, 98% accurate to the intended final watches, we can do the last fine-tuning in pre-production. In that case, I will run the presale not too long from now, likely in spring 2024. Of course, if the samples aren’t quite there yet, I will revisit the design/manufacturing first. I have written a ton about the watch itself but not a lot about the inevitable commercial side of it, so let me spend some words on that here.
I can do an initial production run of 300 pieces, 100 of each color. Those will be available through my online shop on a presale basis. The success of this one-week presale window will determine if the project goes through. If not, all orders will be instantly refunded, and I will have to write a VPC eulogy as the final installment of Building A Watch Brand. In case of success, production will start, and deliveries can be expected within the same year, 2024. In that case, I will also start developing a second model to keep the momentum. My dream is to build a small but high-quality watch company, so I will build on the foundation I have laid this year.
To maximize my chances, I am currently planning photography and videography. I am also arranging some exposure outside of Fratello, including third-party reviews. I’d love to get some samples into the hands of people whose opinions are valued by the community. Hopefully, that will help those interested determine whether I have succeeded in making something truly impressive. I am not paying or handing out free watches for reviews, so it is a bit of a search to find independent watch experts with some reach who do it for the love of watches or on alternative income streams. Rest assured, I have some cool ones lined up already, though.
Closing thoughts on ultra-hard coating and the other updates
I am happy that I could finally share the last feature update on the ultra-hard coating. I didn’t want to overpromise as long as I hadn’t secured a technology and a deal just yet. Now that everything is lined up, I am confident enough to share that it will be on the VPC Type 37HW. Equally, I feel the slightly remodeled bezel and the inevitable hurdles were worth sharing with you. As a last bit of news, I can now also finally confirm that I will indeed meet my intended €3K price point, albeit only just. The watch will come in at €2,479 before VAT and shipping. In the Netherlands, that puts it right at that €3,000 mark with VAT included. I work at roughly one-third to one-fourth of the margin of mainstream brands, which should tell you roughly what kind of quality level to expect.
The coming weeks are all about building the required backend for my website and planning the photo and video shoots. I am sure a few more unexpected challenges will come up, which are all part of the game. The nerves will probably only get worse for the foreseeable future as well. Waiting to see how the watch comes out as well as having my entire financial well-being pending on one presale week are weighing heavily on me. But hey, I wanted a challenge…and I found one!
For now, let me thank you for following my journey throughout 2023! If you had told me back in January that I wouldn’t be holding a physical watch at this point yet, I would have probably been shocked. But we are getting super close now, dear Fratelli! Let’s get it in 2024! Have an absolutely lovely new year, and we’ll meet again in 2024!
Can’t get enough?
- VPC website and newsletter opt-in
- VPC on Instagram
- Building A Watch Brand Episode 1 — Introduction
- Building A Watch Brand Episode 2 — Brand and name
- Building A Watch Brand Episode 3 — Finances, risk mitigation, and a designer
- Building A Watch Brand Episode 4 — Unveiling the watch concept
- Building A Watch Brand Episode 5 — The first design ideation sketches
- Building A Watch Brand Episode 6 — Caliber, pouch, case and bracelet updates, typography
- Building A Watch Brand Episode 7 — Dial design
- Building A Watch Brand Episode 8 — Geeking out on typography
- Building A Watch Brand Episode 9 — 3D Modeling, Tech Development, And Opening Up On The Mentally Challenging Side
- Building A Watch Brand Episode 10: From design to manufacturing
- Building A Watch Brand Episode 11: Manufacturing — The watchmaker’s tools come out