How Watches Work: What Is CVD Coating?
Another day, another term that we see and hear, but maybe don’t know what it means. Today, it’s CVD. Well, what is CVD? As you probably guessed, CVD is an abbreviation. It stands for Chemical Vapor Deposition, a type of coating process that is not to be confused with PVD (Physical Vapor Deposition). Please note that this is a coating “process” rather than a coating itself.
CVD-applied coatings are commonly found throughout the industry in many different consumer products. CVD-applied coatings are found in a range of applications that require a high-performance thin-film coating. But, what is it about the chemical deposition process that makes a superior coating for high-performance precision applications such as watchmaking?
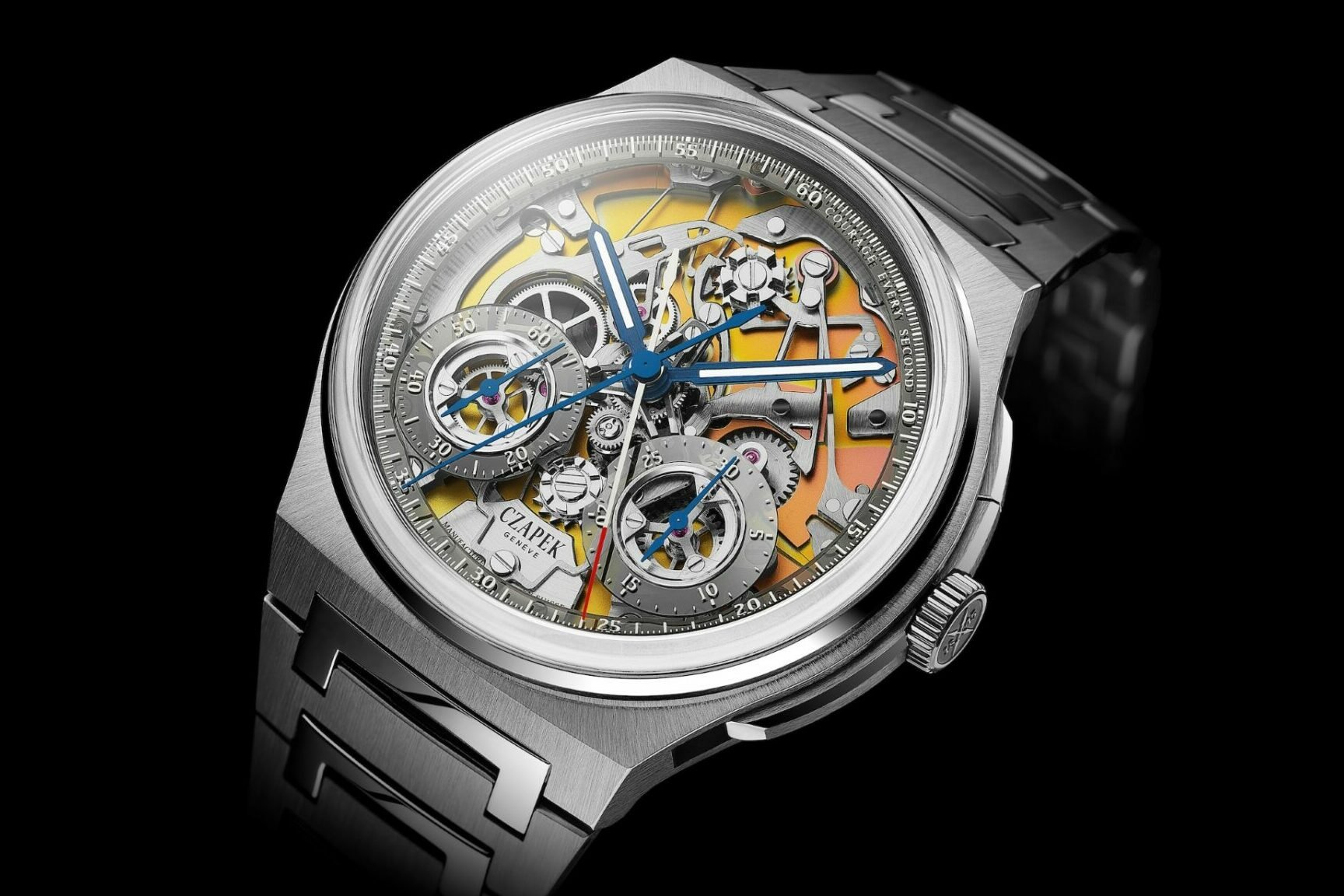
The Czapek Antarctique Rattrapante for Only Watch 2021 used a CVD-applied coating for the orange split-second main plate
How are CVD coatings applied?
Chemical vapor deposition is a process that involves the reaction of a volatile precursor, which is injected into a chamber, typically under vacuum. This chamber is heated to a reaction temperature, and this causes the precursor gas to react or break down into the desired coating and bond to the material surface. Coating material builds on the surface over time, creating a coating throughout the surface of the exposed part.
Why should I use CVD?
A key reason for using the CVD process lies in the fact that the reactants used are gases, thereby taking advantage of the many characteristics of gases. One result is that CVD is not a line-of-sight process like most other coating processes. Therefore, it can be used to precision coat intricate surfaces, including seal areas and internal surfaces like screw threads.
CVD also offers other advantages over other deposition processes. These include various base coating materials, including metals, alloys, and ceramics. The precursor gas can easily be optimized for specific characteristics such as wear resistance, corrosion resistance, or chemical resistance. Additionally, due to the structure of the coating process, many parts can undergo coating simultaneously, making the production more economical when compared to other vapor deposition processes.
Why shouldn’t I use it?
But it’s not all sunshine and rainbows, and this method is not universally the best process for all use cases. It has some drawbacks that might make it less appropriate for some applications. Due to the nature of the reactant gases, masking areas is nearly impossible. CVD-applied coatings are pretty much all or nothing. Additionally, the high temperatures required for the process mean that some surface materials cannot withstand CVD-applied coatings. For example, these temperatures usually exceed the tempering structure for stainless steel. So steel watch cases would need to be rehardened afterward, increasing the cost and reducing the practicality of a CVD-applied coating in that instance. That said, some brands have used CVD-applied coatings for watch cases, but PVD-applied coatings are more common.
So there we have a summary of the CVD coating process. There’s a whole lot of science involved with coatings, as I’m sure you’ve realized if you’ve been following along with my previous articles on coatings. Hopefully, this article has given you an insight into its key advantages and disadvantages and how it differs from similar coatings such as Ion-Plating or DLC.
Follow me on Instagram: @davesergeant | @fratellowatches